Fibretrace x Nobody Denim
Grown On Australian Soil, Made By Australian Hands
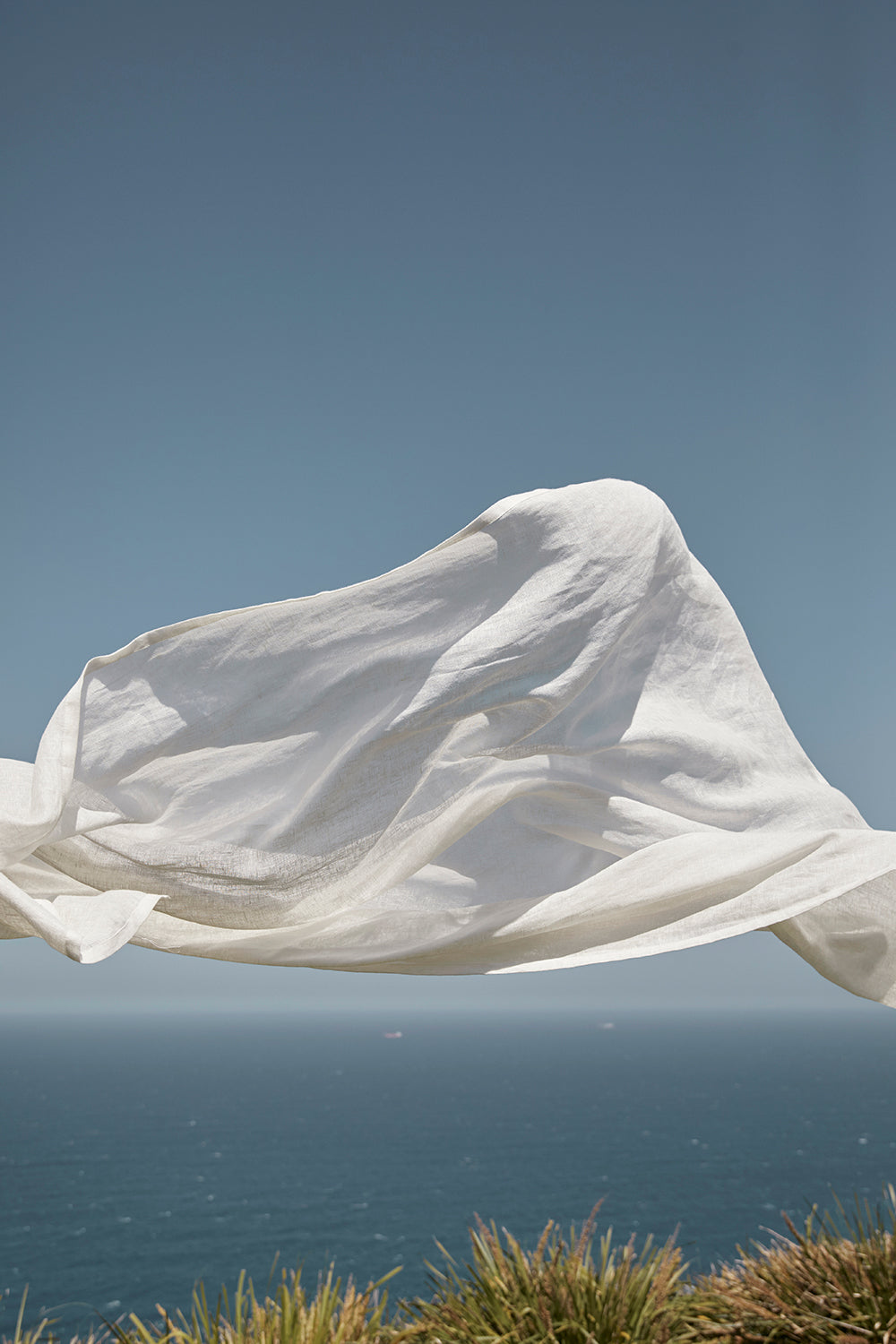
The First Certified Carbon Positive Denim Collection.
Nobody Cares - we care about our impact, and we want to empower our team and customers to contribute to improved environmental production standards.
We can’t do this without the power of transparency.
We are proud to partner with FibreTrace, an indestructible transparency technology that follows our product from raw fibre source right through to finished product.
FibreTrace was built on the belief that every fibre tells a story… the Nobody Denim and FibreTrace collection tells the story of Good Earth Cotton.
This collection is grown on Australian soil, and made by Australian hands.
Grown in Moree, New South Wales, Australia by the Statham family, second generation cotton farmers.
The Statham family have been committed to implementing best practice farming such as using organic composite waste matter, extensive use of solar and renewable energy, crop rotation, minimal tillage (or turning) of the soil and ensuring the surrounding valley supports growth of native vegetation - it is home to more than 42,000 birds representing 47 species.
As a result, the cotton plantation has been independently certified as carbon positive, meaning its growth actually reduces carbon emissions in the atmosphere. Hence its name, Good Earth Cotton.
FibreTrace technology is embedded into the raw cotton, and then through the power of blockchain technology is scanned at every stage throughout the supply chain right back to our Melbourne facility where our Nobody Denim designers and makers proudly make and launder the finished product just for you.
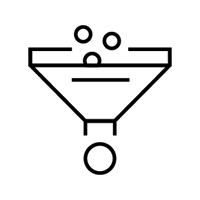
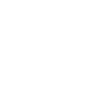
FibreTrace embeds, scannable, luminescent pigments into any fabric, right at raw materials(e.g. farm) or spinning mill.
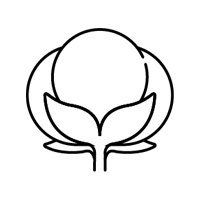
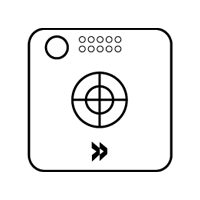
FibreTrace is embedded into Good Earth Cotton at the cotton gin, straight from the farm.
A small hand held FibreTrace scanning device is than utilised to scan the cotton as it’s baled up, confirming that specific cotton is 100%.
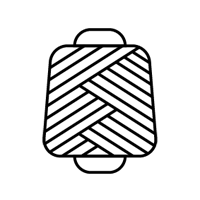
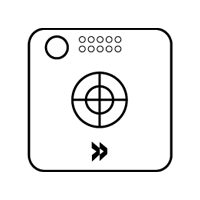
The raw cotton arrives at the spinner and is scanned again to verify it’s Good Earth Cotton.
It’s then spun into yarn.
The yarn is scanned prior to shipping, and recorded on the blockchain.
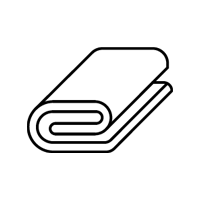
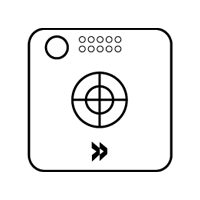
The yarn is scanned on arrival at the fabric mill, verifying it’s Good Earth Cotton and tracking the movement of the product.
Once the fabric is woven, again it’s scanned to verify content of Good Earth Cotton and record the journey on the blockchain.
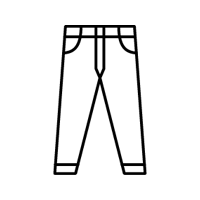
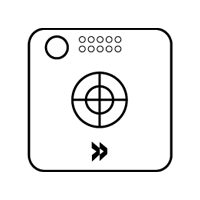
When the fabric arrives back to us at Nobody Denim in Melbourne we scan it to confirm the Good Earth Cotton cotton and record the product movement.
From here we cut the fabric, carefully and skilfully construct the product, launder it for the perfect finish and package it ready to sale.
The product is scanned one last time to record the journey before it is ready for you.
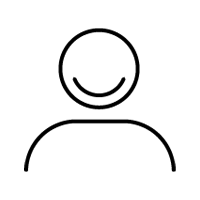
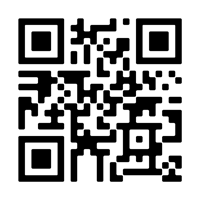
Each of our FibreTrace verified products is marked with a QR code on the swing ticket which you can scan, and on the Nobody Denim website we share the entire product journey with you.
RELATED PRODUCTS
The first carbon positive denim collection has arrived in light authentic indigo.






At Nobody Denim, honest and sustainable business is good business. Ethics are at the heart of what we do. We’re on a never ending journey to improvement. We believe in a triple bottom line approach that sees people and the planet as integral to our decision-making and direction. FibreTrace is helping us on the next steps of that journey, and here you can learn how our product comes to life from beginning to end.
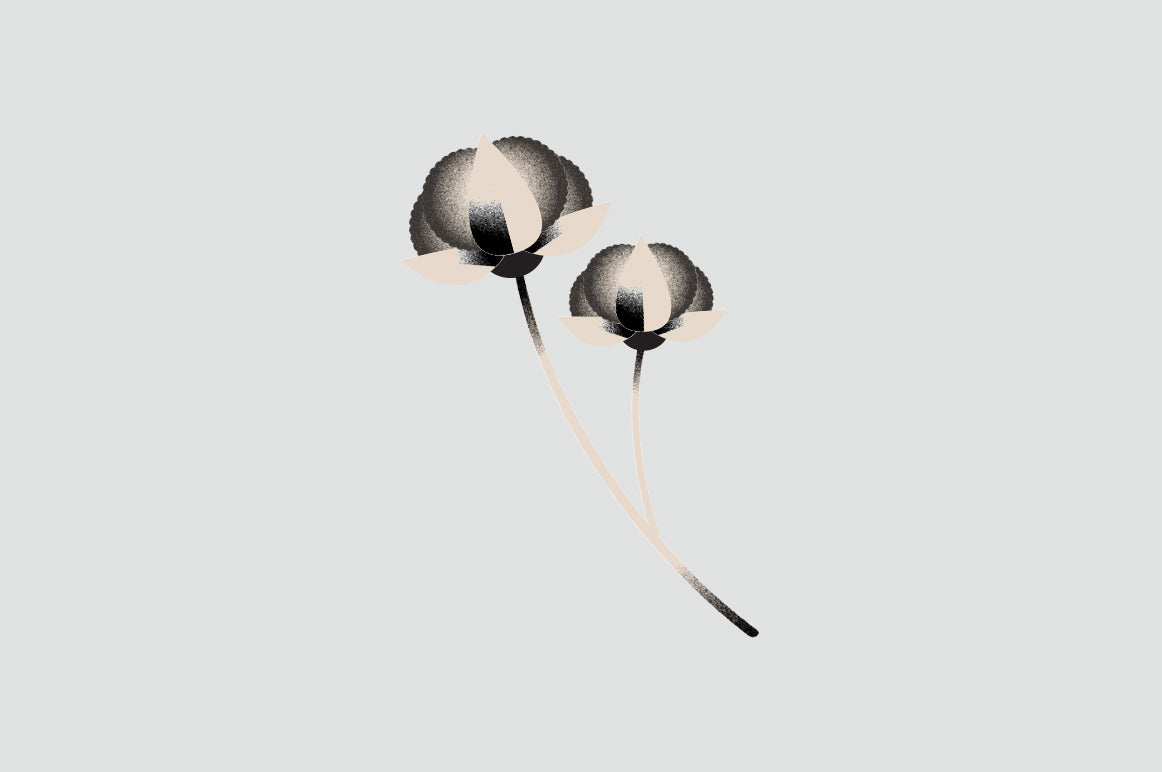
CARBON POSITIVE COTTON
Good Earth Cotton grown in Moree, New South Wales by Sundown Pastoral Company team at Keytah Station.
Picked by James Skehan.
Good Earth Cotton is the first carbon positive cotton farm in the world, we are so proud to use Australian cotton grown and cared for by Australian hands.
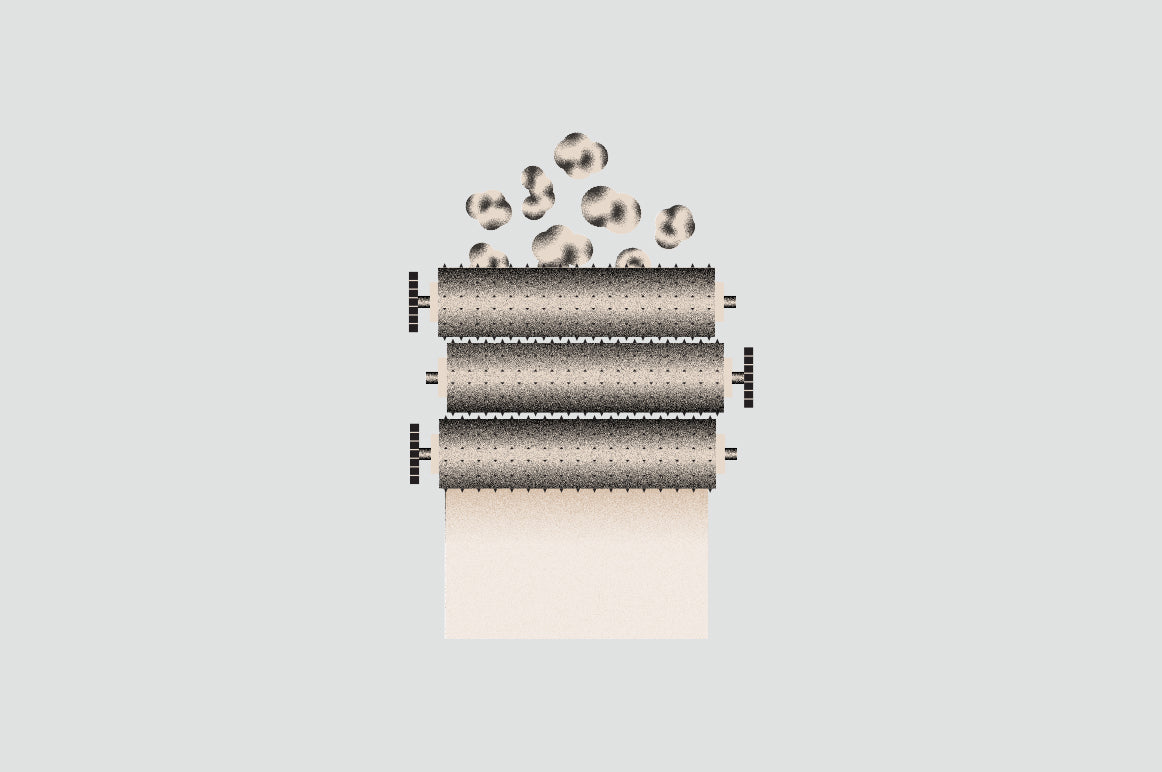
GINNING THE COTTON
Ginned in Moree, New South Wales by Wathagar Ginning Company.
Ginned by Mike Murray.
From the field, seed cotton moves to nearby gins for separation of lint and seed. The cotton first goes through dryers to reduce moisture content and then through cleaning equipment to remove foreign matter. It is then compressed into bales in preparation for shipping.
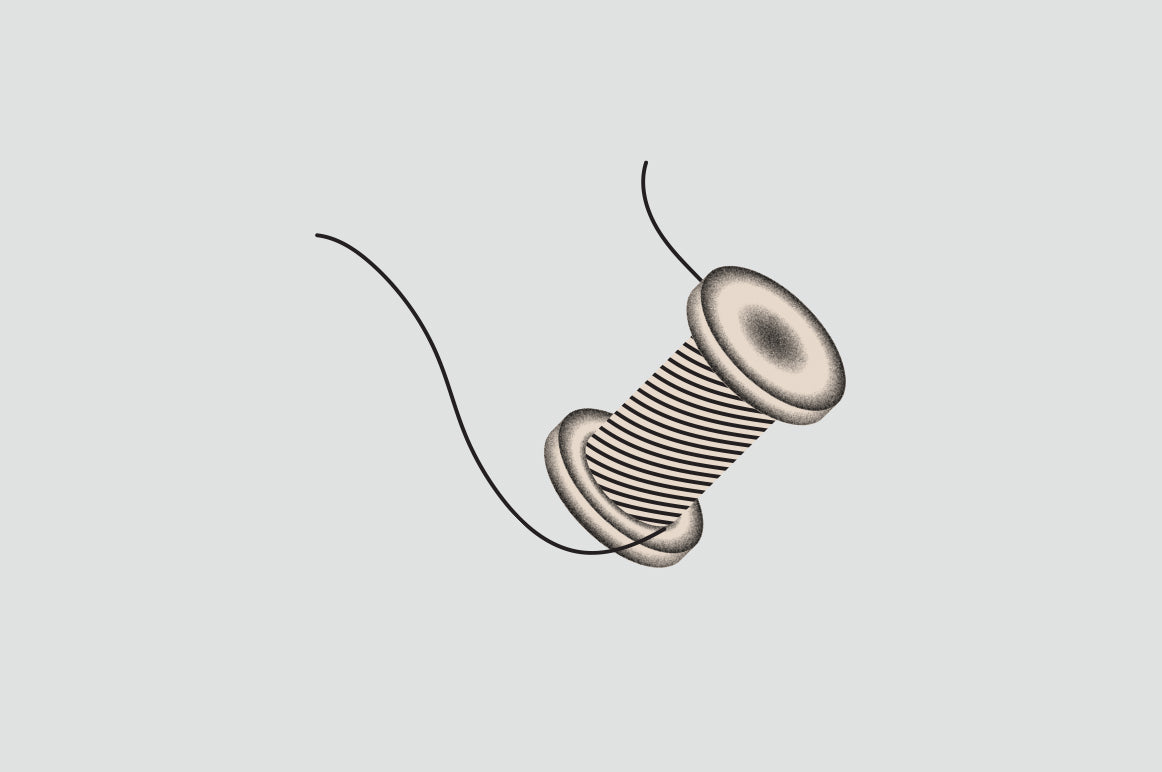
SPINNING THE YARN
Spun in Istanbul, Turkey by Orta Anadolu.
Founded in 1953, Orta has been weaving a denim heritage passed from generation to generation ever since. Orta is committed to transparency and trustworthiness - working hand in hand with brand partners to improve manufacturing processes that focus on spinning better cotton for the earth and reducing waste output.
After carefully choosing the finest cotton, Orta spins a unique Good Earth Cotton yarn and incorporates elastane in the core of the yarn (right in the centre) to ensure stretch and recovery of the fabric, ensuring the ultimate comfort.
After spinning, the yarns are tightly wound around bobbins or cones and are ready for fabric forming.
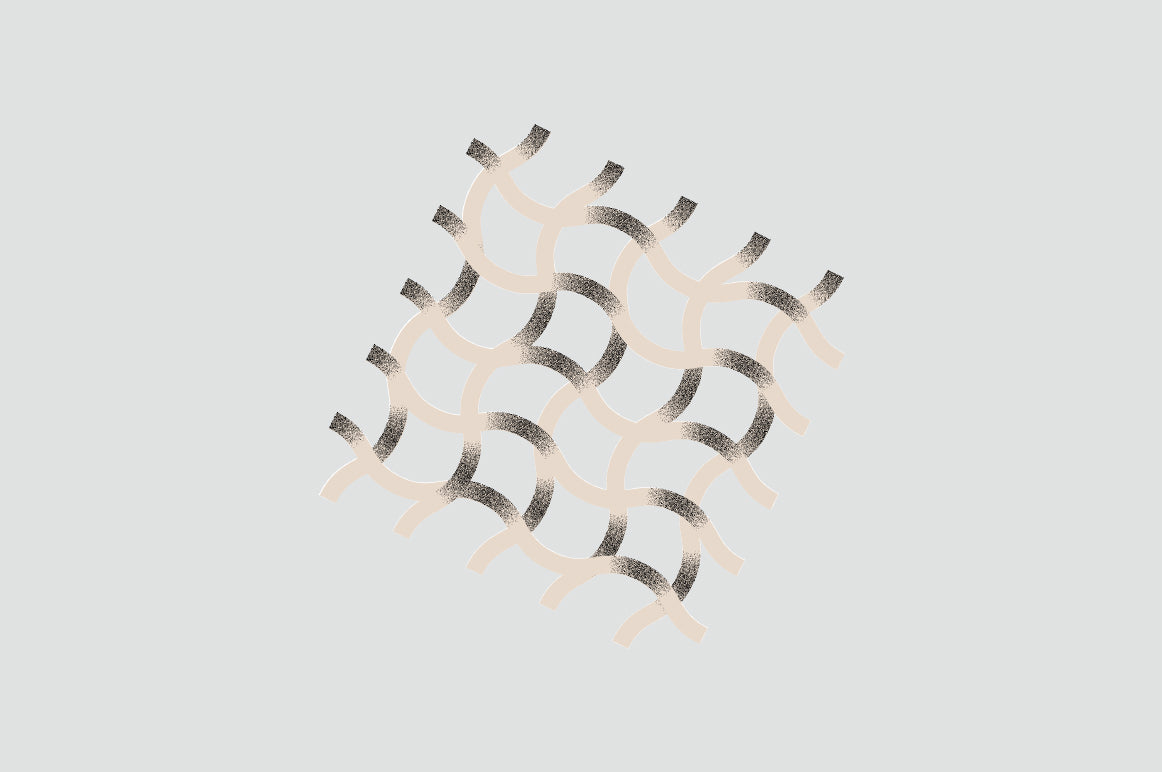
WEAVING THE FABRIC
Woven in Istanbul, Turkey by Orta Anadolu.
Weaving is the oldest method of making yarn into fabric.
On the loom (or the weaving machine), lengthwise yarns called the warp form the skeleton of the fabric, then the filling (better known as the weft) yarns are interlaced widthwise to form the denim fabric.
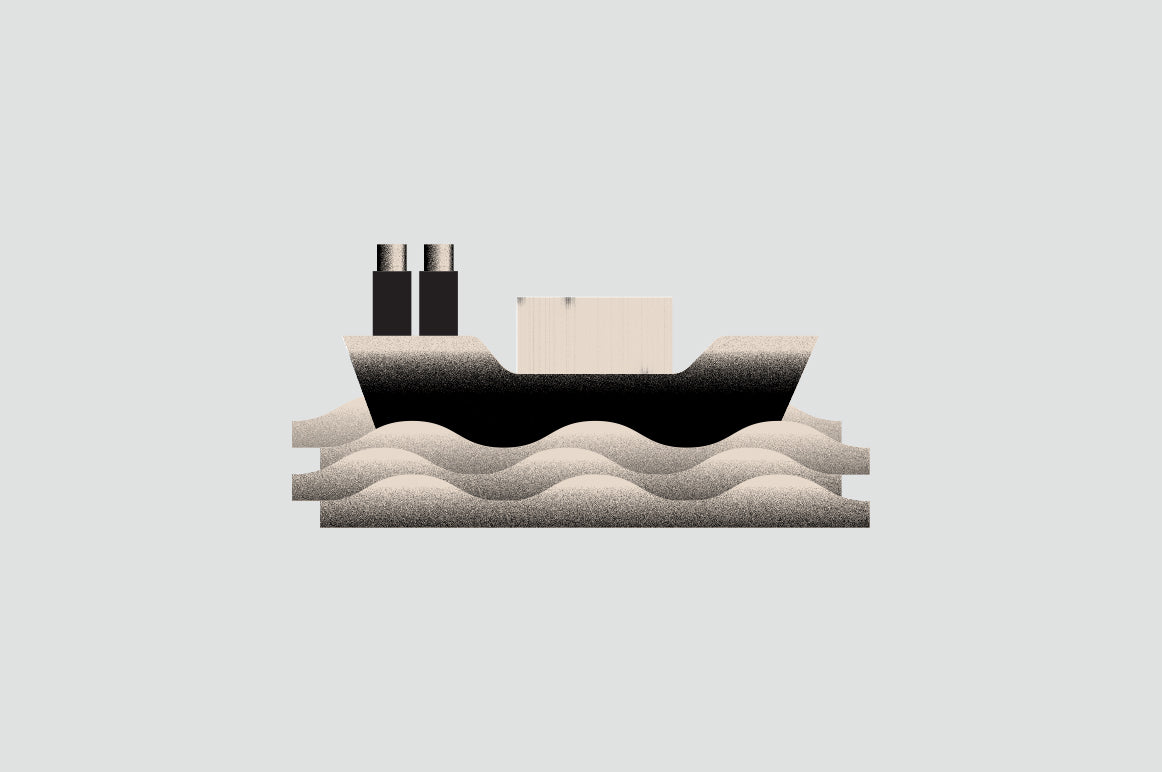
Denim is Shipped
Shipped.
The denim is shipped by sea to the Nobody Denim factory, located in Thornbury, Melbourne.
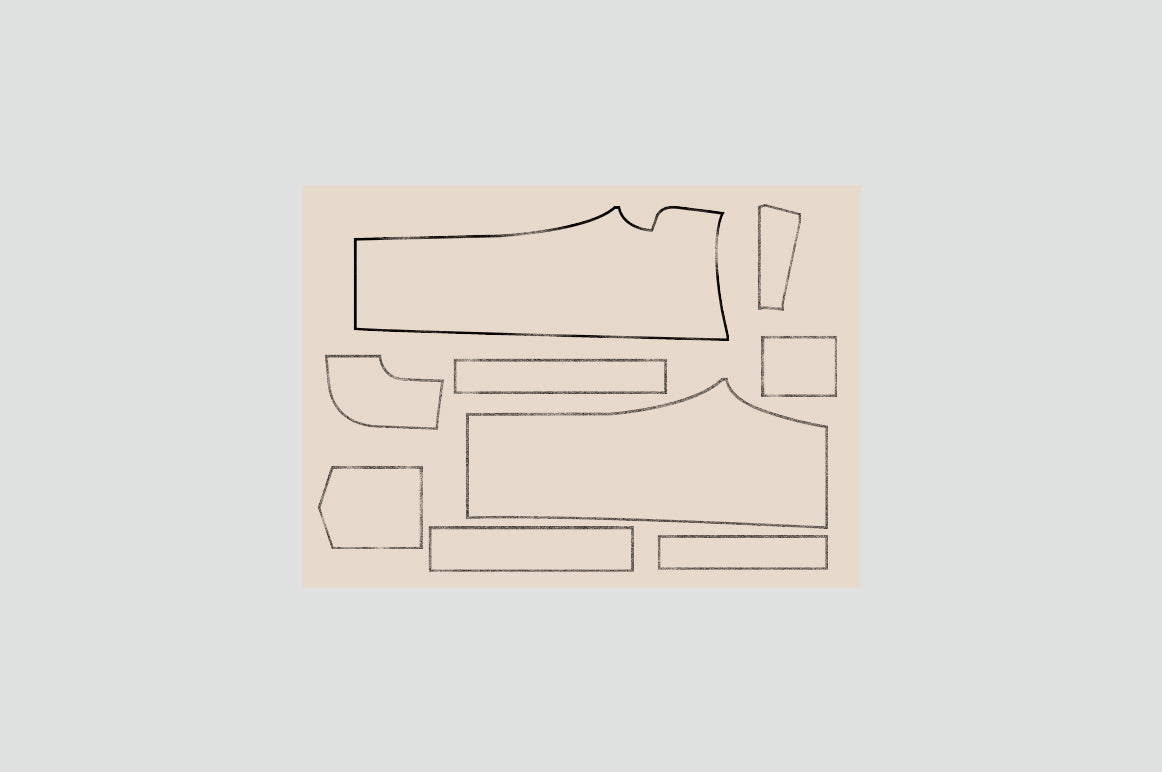
Denim is Cut
Cut in Thornbury, Melbourne Victoria by Nobody Denim.
The denim fabric is laid out in stacks, as many as 30 layers thick. The pattern for our Nobody Denim jeans are placed on top of the stack and a high speed cutting machine is used to cut the denim. Excluding rivets, buttons and zippers, a pair of traditional 5 pocket jeans contains about 17 different pieces, from the pockets to the leg panels, to the waistband and belt loops.
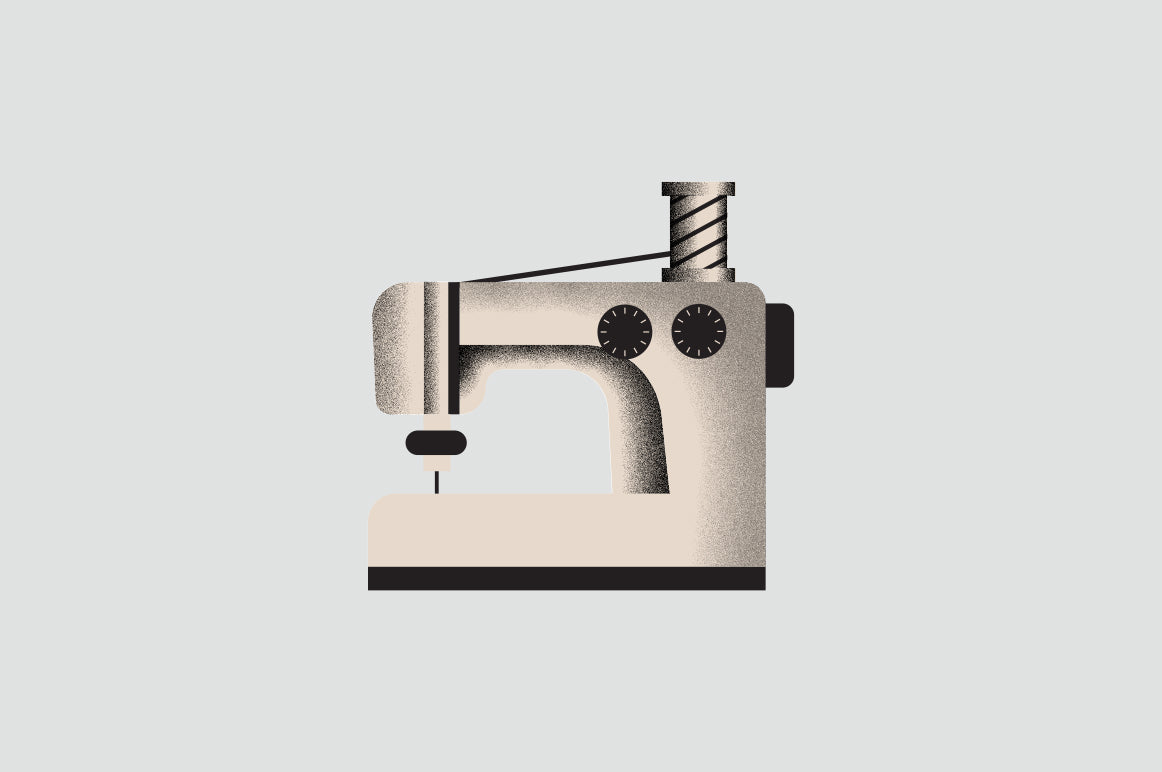
Denim is Hand Sewn
Sewn in Thornbury, Melbourne Victoria by Nobody Denim.
Our skilled makers use machines with extreme precision and attention to detail to piece together the various parts by hand and create the basic outline of the jeans. Sewing is done in an assembly line fashion, with rows of industrial human-operated sewing machines. Each sewer is assigned a specific function, such as making only back pockets. First, the various pockets are assembled. Next, one sewer attaches the pockets to the leg panels, another attaches fly pieces & zippers, another then sews the leg seams together, and still another attaches the waistband. Lastly the hems are sewn & beltloops are attached ready for the jeans to be washed at our Laundry.
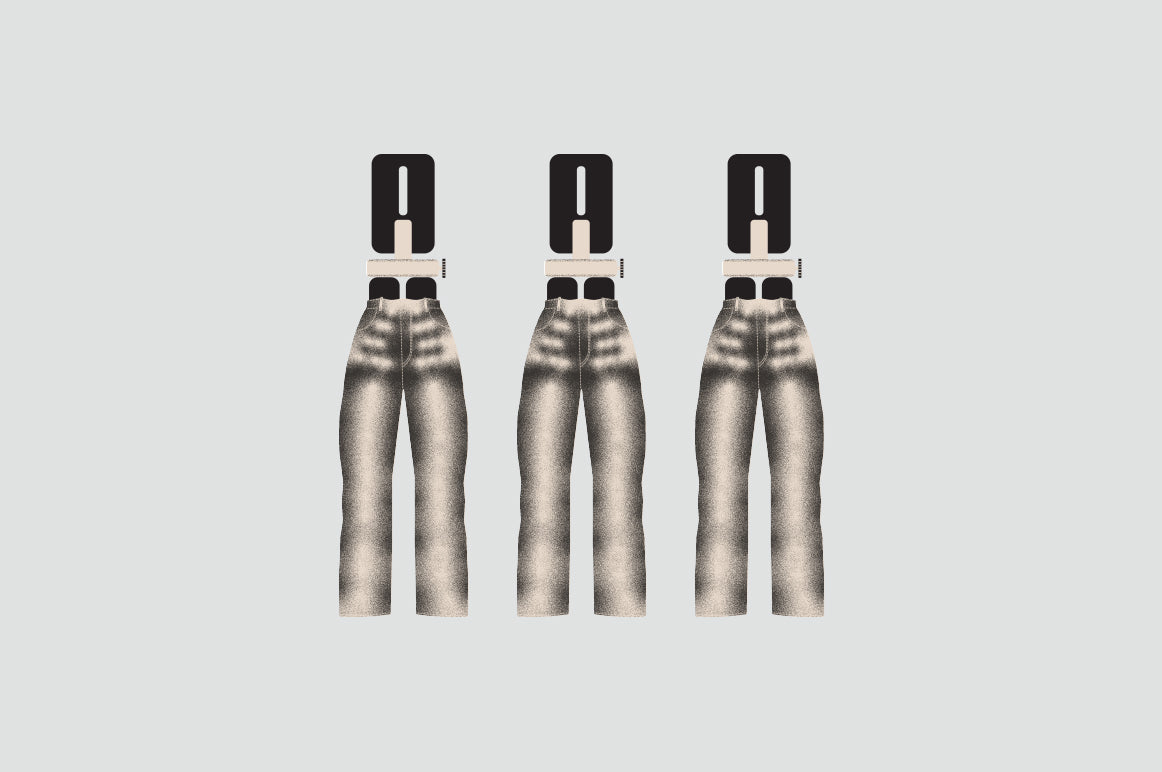
Jeans are wiskered and brushed
Treated in Fitzroy, Melbourne Victoria by Nobody Denim.
Jeans are transported to our Laundry in Fitzroy, Melbourne where the jean is then mounted on our inflatable dummy. Here our machine operators use specialised tools to wear away the surface indigo in areas that would usually be 'worn' in over time. These techniques are called 'Whiskering', where natural creasing would be revealed over time, and 'Brushing', where a natural fade would appear over time. These brushed areas are not revealed until the garment is washed.
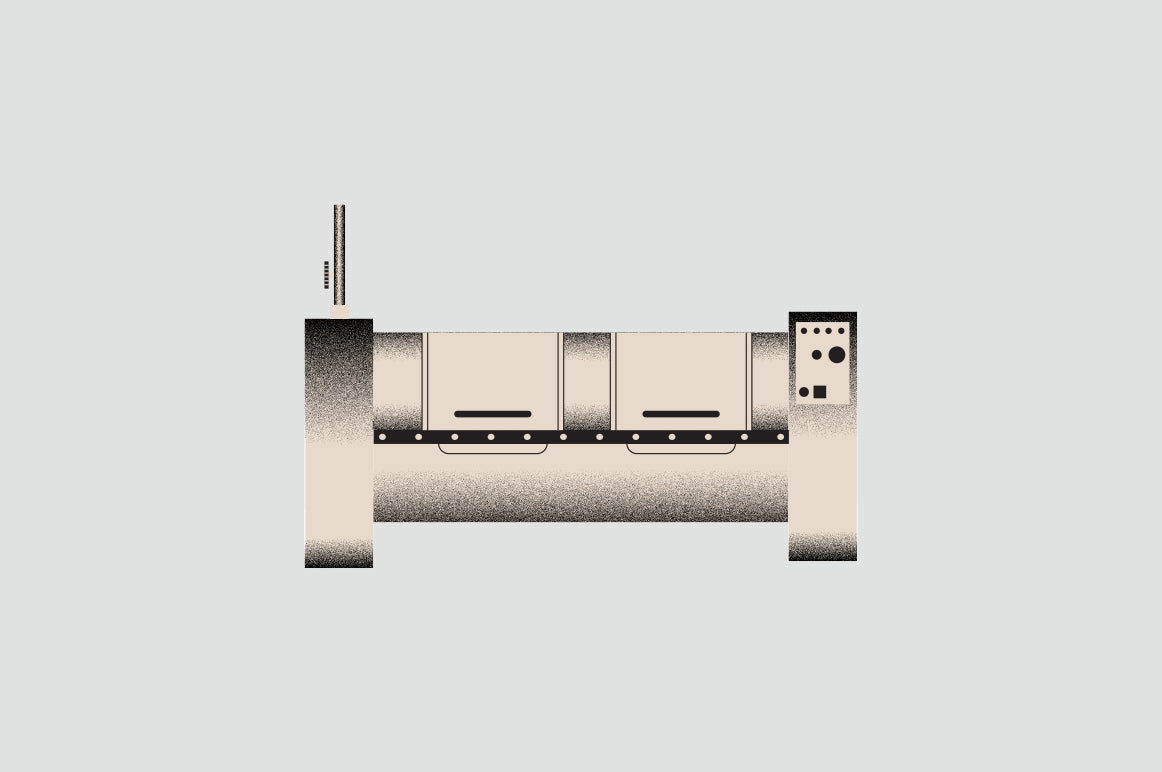
Jeans are washed
Washed in Fitzroy, Melbourne Victoria by Nobody Denim.
The jeans then go through at least 2 washes. The initial first wash is called 'desize' which takes the shrinkage out of the garment .Next the jeans are put through a stone and/or bleach wash cycle. One fabric quality can be utilised across various shades of indigo (from light to dark) by using different levels of stone and bleach.
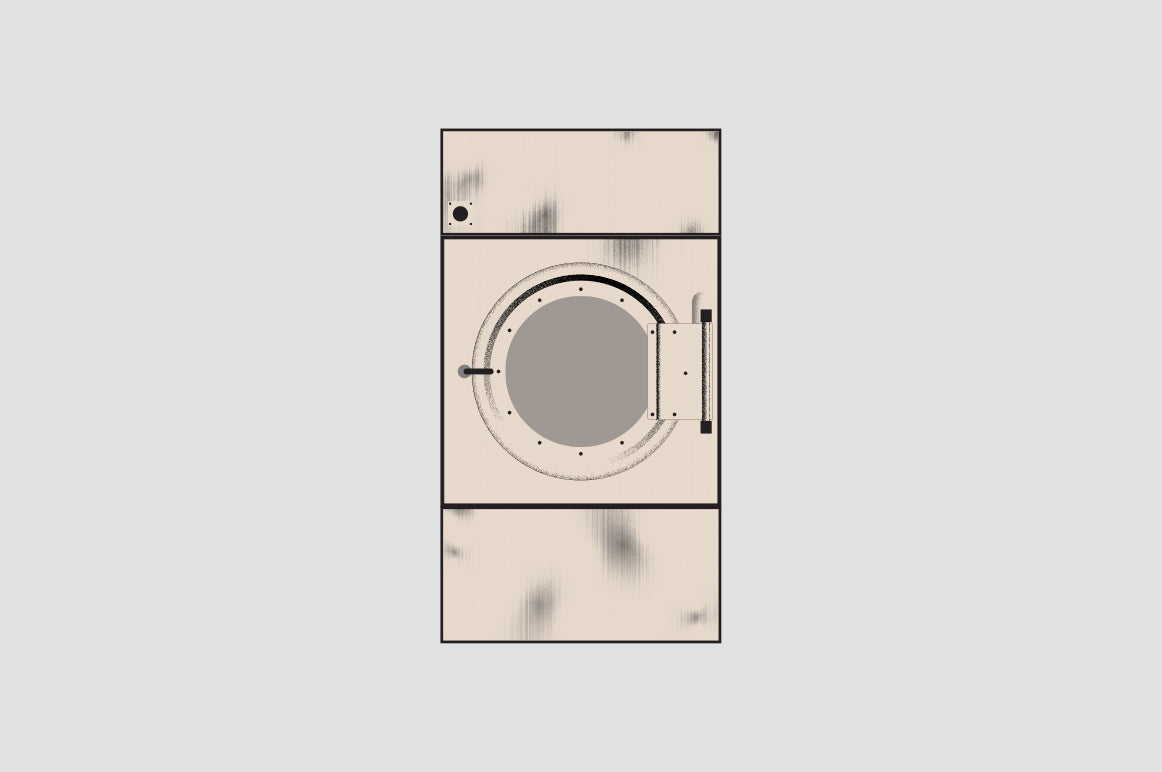
Jeans are Dried
Dried in Fitzroy, Melbourne Victoria by Nobody Denim.
The Jeans are dried in our industrial dryers.
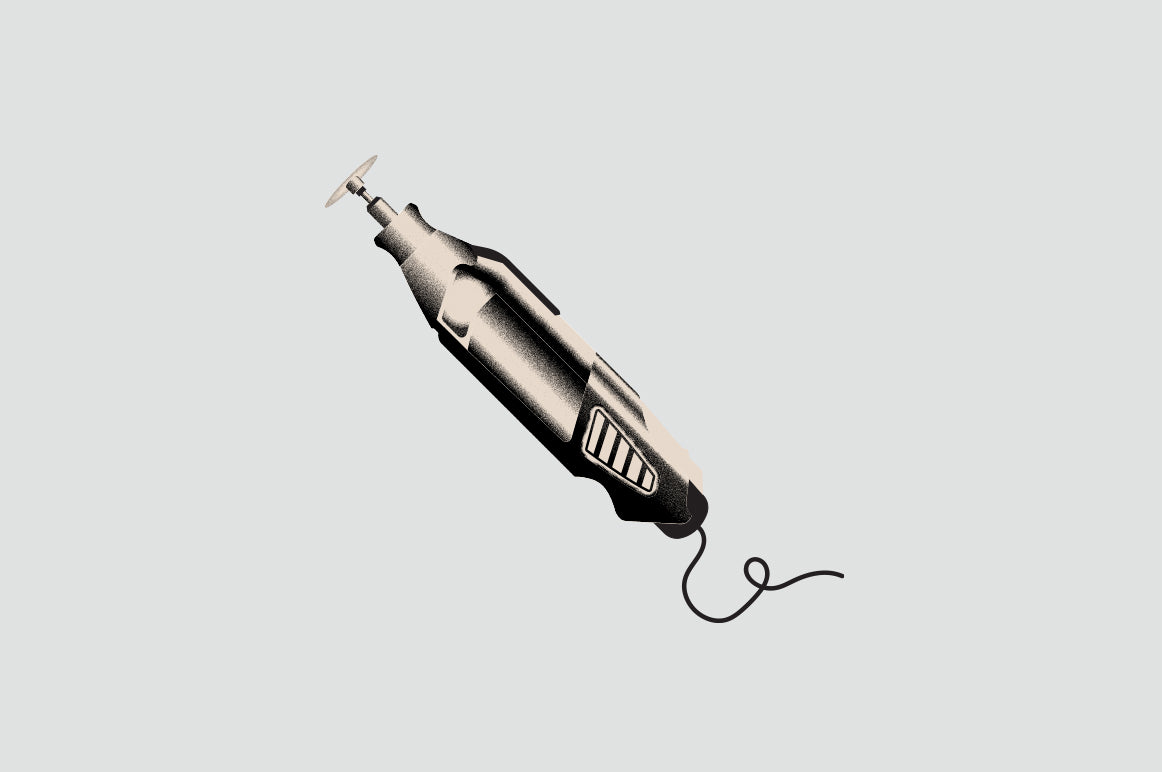
Jeans are Distressed
Dremeled in Fitzroy, Melbourne Victoria by Nobody Denim.
Further distressed with a dremel tool. The dremel tool is used to add holes and grinding, specifically designed to each and every style.
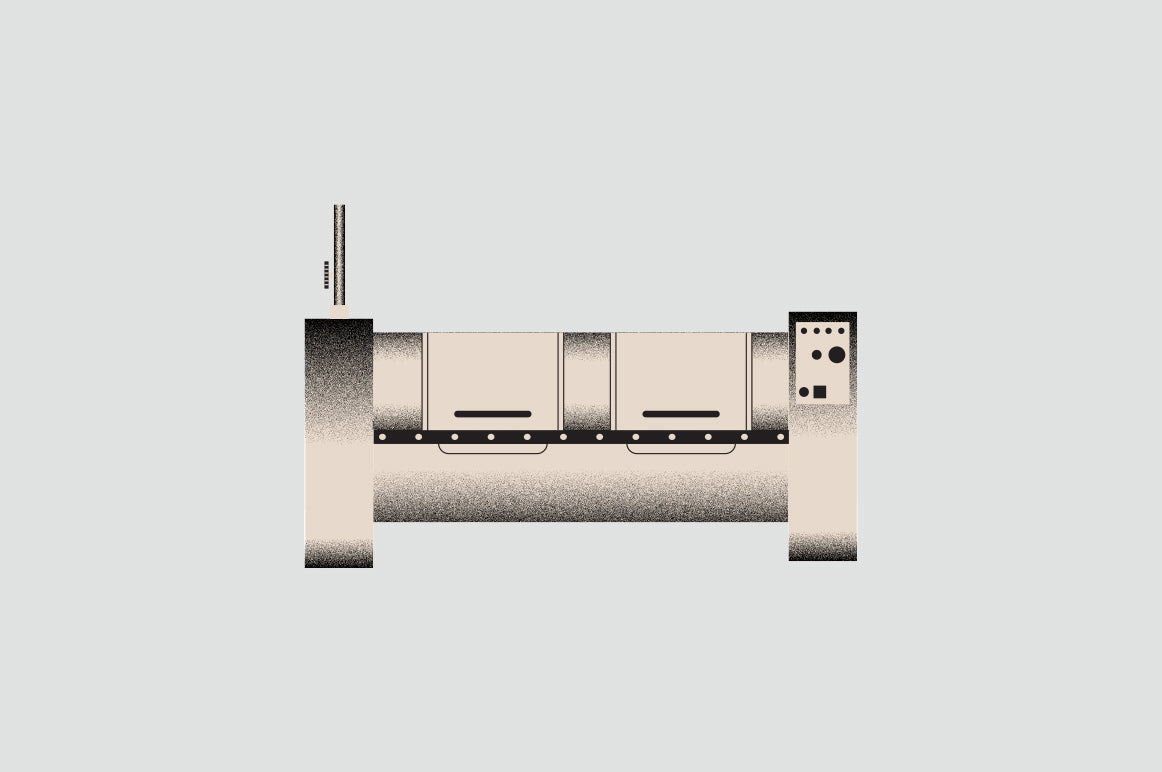
Jeans are washed again
Finished in FItzroy, Melbourne Victoria by Nobody Denim.
Final wash process to remove any detergent. After the final wash, the weft yarns are left behind leaving white yarns where the disressing & destruction has been applied.
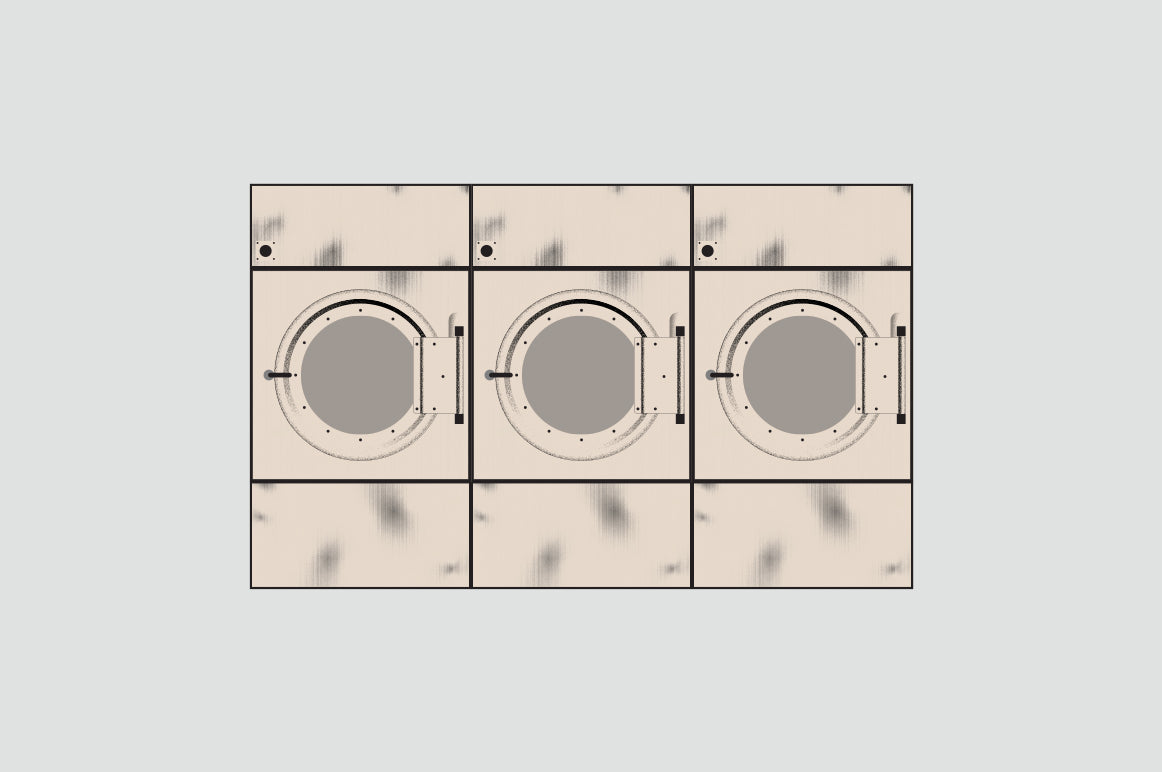
Jeans are dried again
Dried in Fitzroy, Melbourne Victoria by Nobody Denim.
The jeans are once again dried in our industrial driers
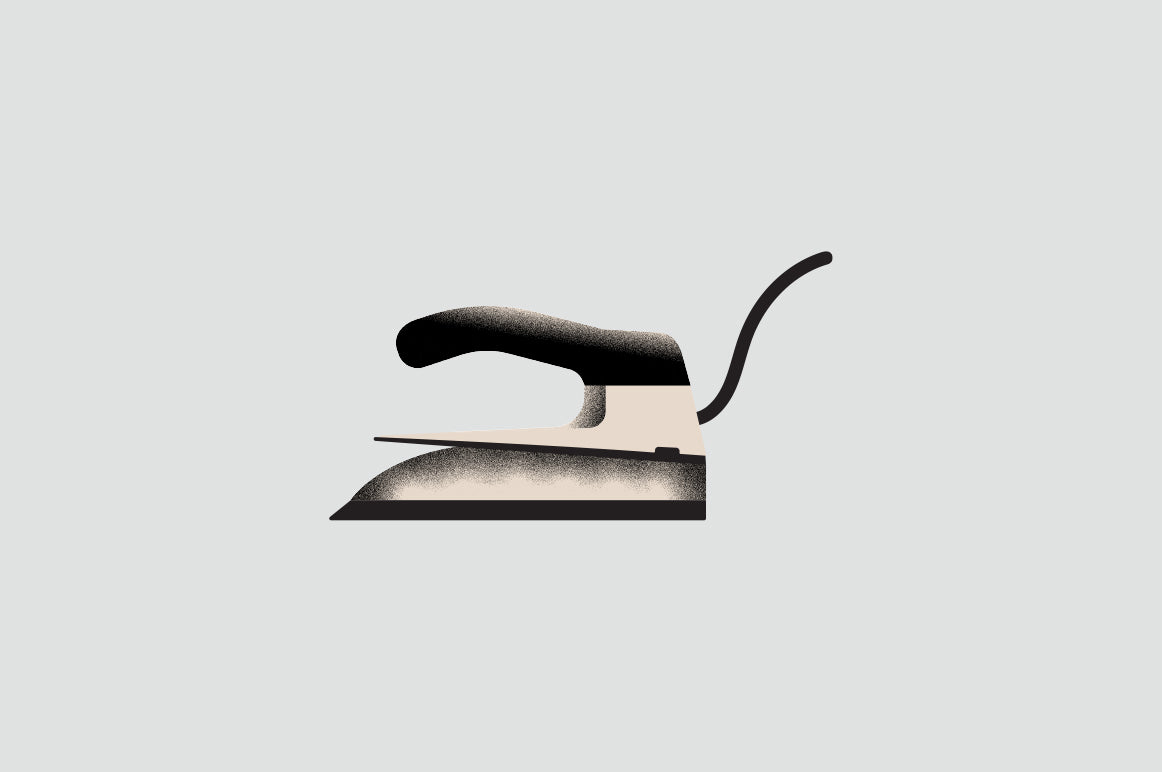
Jeans are pressed
Pressed in Fitzroy, Melbourne Victoria by Nobody Denim.
The completed pair of indigo jeans is then professionally pressed using industrial steam irons. Some styles are pressed by hand while others are placed into a large pressing machine that steam presses the entire garment at once.
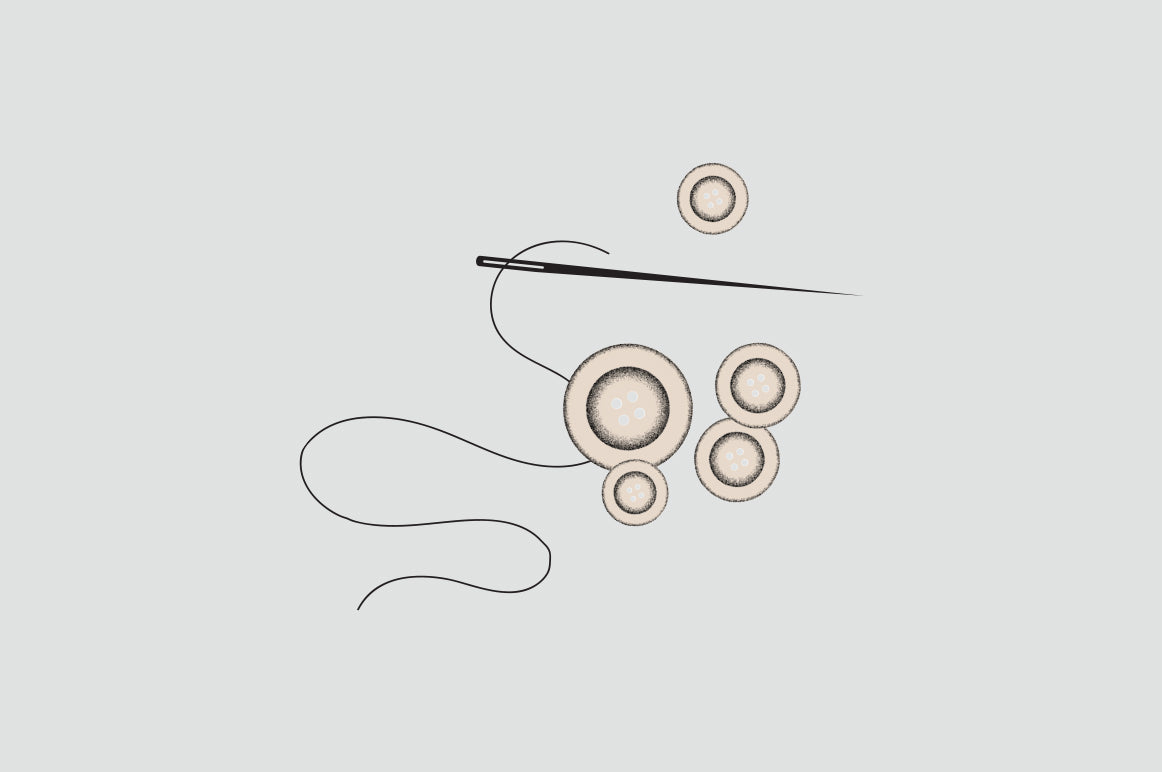
Buttons and hardware
Hardware put on in Thornbury, Melbourne Victoria by Nobody Denim.
Our jeans are returned to Thornbury to have loose threads and frayed edges trimmed, as well as buttons & rivets attached.
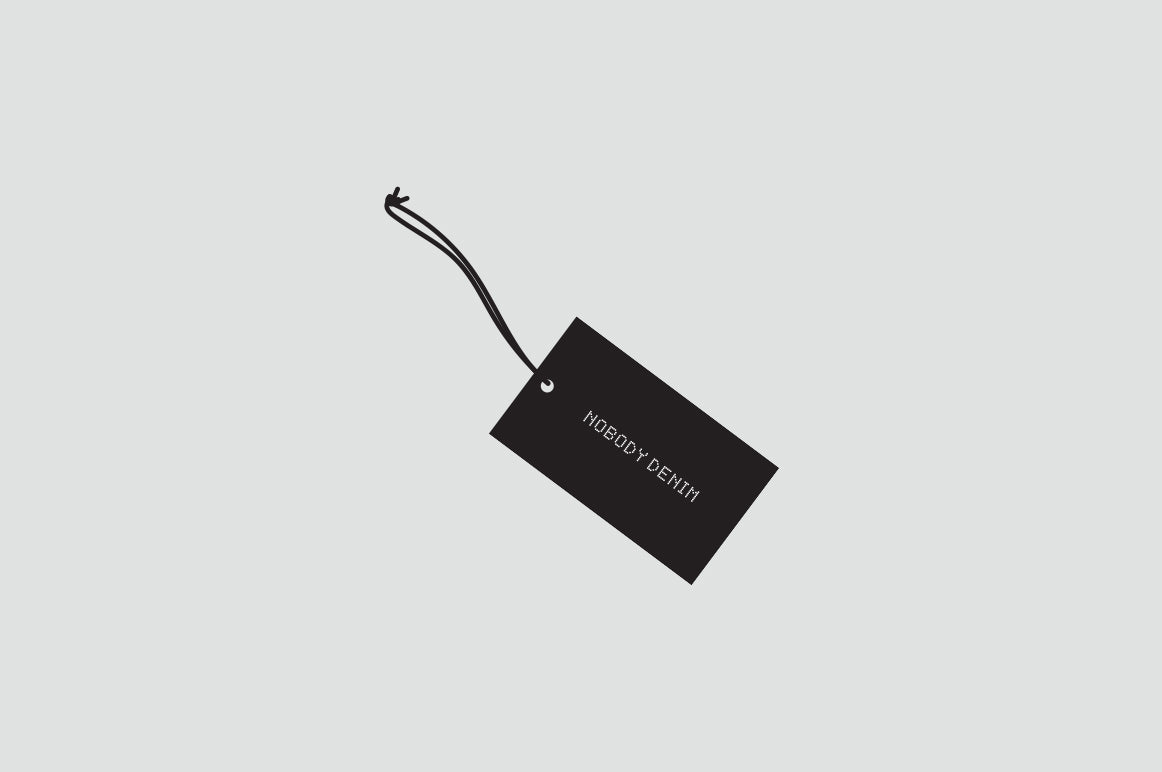
Labelled and tagged
Tagged in Thornbury, Melbourne Victoria by Nobody Denim.
The final touches are added. Swing tickets and labels are applied ready to be dispatched to stores.